Introduction
This article explores how AI-driven planning and scheduling can help component manufacturers produce better, outlines a structured approach for successful implementation, highlights potential challenges, and discusses the outcomes that can be achieved.
The Solution: AI-Based Planning and Scheduling
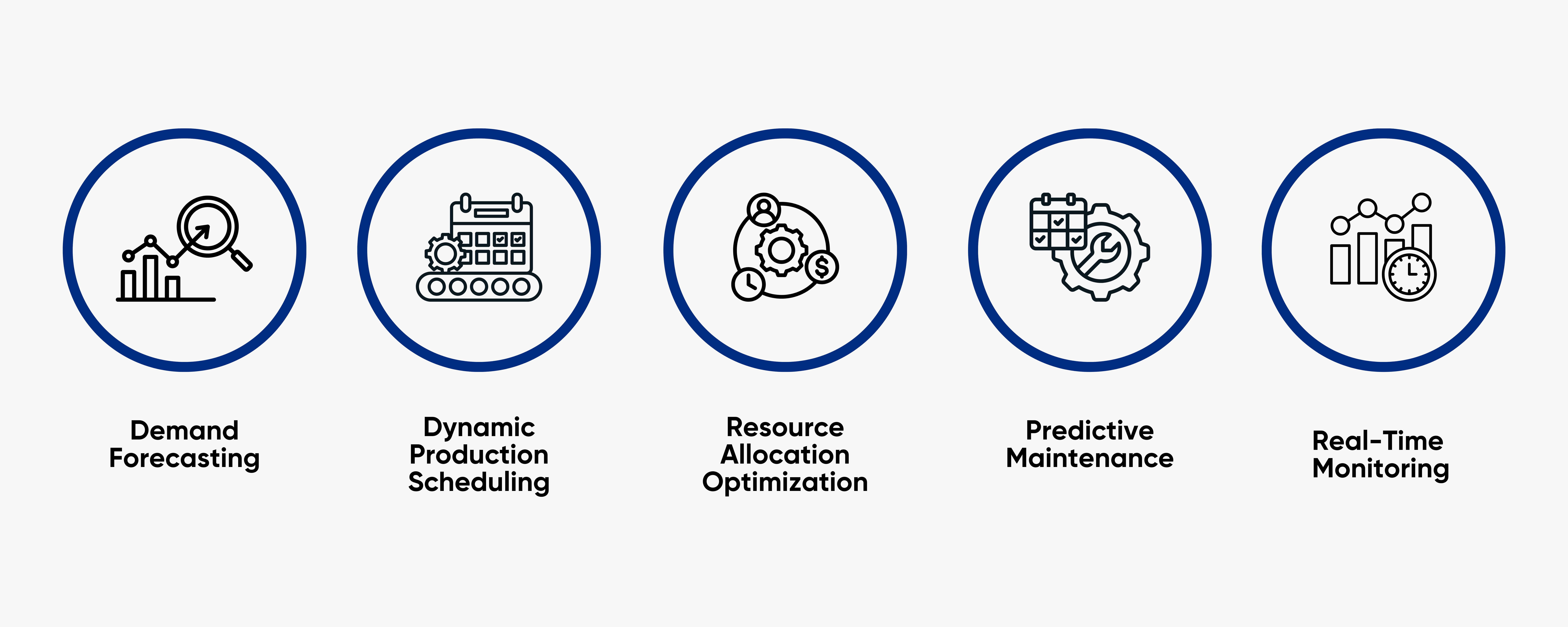
1. Demand Forecasting
- Case Study: According to a report, organizations that implement AI for demand forecasting experience a 30% reduction in inventory costs due to more accurate predictions. This reduction is critical in minimizing excess inventory while ensuring that customer demand is met promptly.
2. Dynamic Production Scheduling
- Case Study: A leading automotive parts manufacturer implemented an AI-driven scheduling system that adjusted production plans based on real-time data from the shop floor. This resulted in a 25% increase in on-time deliveries, significantly enhancing customer satisfaction.
3. Resource Allocation Optimization
- Use Case: Research indicates that companies utilizing AI for resource allocation can achieve a 15-20% reduction in operational costs by improving asset utilization. This improvement translates into significant savings over time.
4. Predictive Maintenance
- Case Study: A manufacturer specializing in electronic components deployed predictive maintenance algorithms that reduced unplanned downtime by 40%, leading to improved overall equipment effectiveness (OEE).
5. Real-Time Monitoring
- Case Study: A large-scale automotive manufacturer implemented real-time monitoring systems, which enabled them to reduce cycle times by 15% and improve throughput rates by identifying and addressing bottlenecks in production processes swiftly.
How AI-Based Solutions Help Component Manufacturers
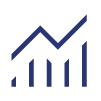
Enhanced Production Efficiency
By optimizing resource allocation and scheduling through AI-driven insights, manufacturers can achieve higher throughput rates. Research indicates that companies utilizing AI for production scheduling report up to a 30% increase in operational efficiency.
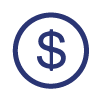
Cost Reduction
Efficient resource management leads to lower operational costs. A study found that organizations leveraging AI for resource allocation experience a 15-20% reduction in costs through improved utilization of assets.
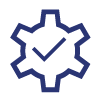
Improved Quality Control
AI-powered quality assurance systems can detect defects during production using computer vision algorithms or sensor data analysis. By enabling immediate corrective actions when anomalies are detected, manufacturers can reduce rework rates and enhance overall product quality.
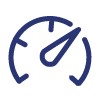
Increased Agility
The ability to dynamically adjust schedules in response to real-time data empowers manufacturers to remain agile in a rapidly changing market environment. This agility is crucial for meeting customer demands without incurring excessive costs or delays.
Approach for Successful Implementation
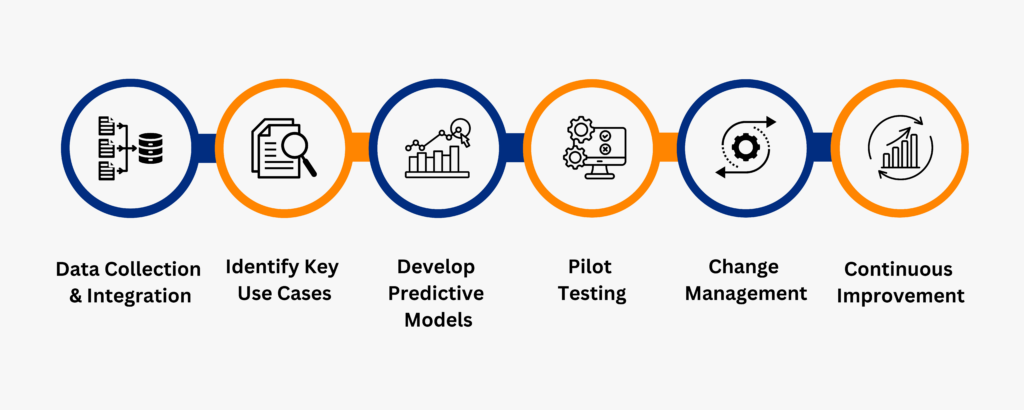
1. Data Collection and Integration
- Gather Historical Data: Collect historical data from various sources such as Enterprise Resource Planning (ERP) systems, production logs, supply chain databases, and market analysis reports.
- Ensure Data Quality: Implement processes for cleaning and validating data to ensure accuracy before feeding it into AI models.
- Integrate Systems: Ensure integration with existing systems for seamless data flow across departments (e.g., sales, operations, finance).
2. Identify Key Use Cases
- Focus on High-Impact Areas: Identify specific use cases where AI can drive significant improvements (e.g., demand forecasting accuracy, production scheduling efficiency).
- Engage Cross-Functional Teams: Involve stakeholders from different departments (data scientists, operations managers) to identify pain points and opportunities for improvement.
3. Develop Predictive Models
- Utilize Machine Learning Algorithms: Develop predictive models using machine learning techniques tailored for manufacturing scenarios.
- Refine Models Continuously: Continuously refine models using real-time data inputs for improved accuracy over time.
4. Pilot Testing
- Implement Pilot Projects: Launch pilot projects in controlled environments to test the effectiveness of AI solutions.
- Monitor Performance Metrics: Closely monitor performance metrics during the pilot phase to identify areas for improvement before full-scale deployment.
5. Change Management
- Prepare Employees for Transition: Provide comprehensive training programs to help employees adapt to new technologies.
- Foster Collaboration: Create a culture of collaboration between IT teams and operations staff to ensure smooth adoption of AI technologies.
6. Continuous Improvement
- Regularly Assess Performance: Establish key performance indicators (KPIs) to measure the success of AI-driven solutions.
- Use Feedback Loops: Implement feedback loops that allow teams to refine algorithms based on user experiences and changing market conditions.
Challenges in Implementation
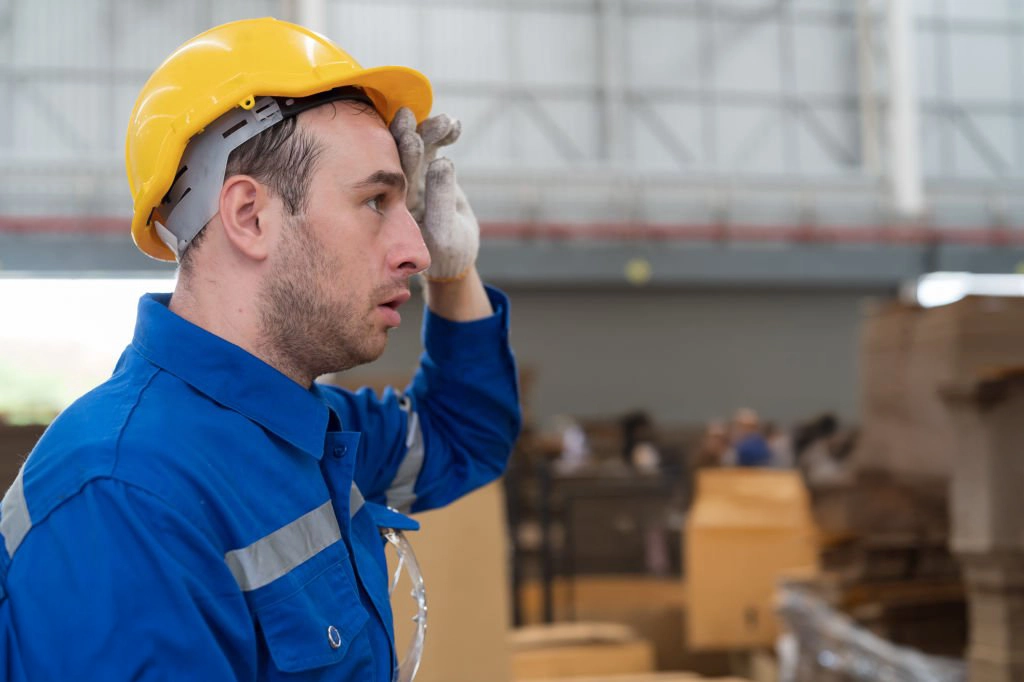
1. Data Quality Issues
- Solution: Implement robust data governance practices that ensure data integrity across all sources before it is utilized by AI systems.
2. Integration Complexity
- Solution: Adopt modular approaches that allow for gradual integration without disrupting ongoing operations.
3. Skill Gaps
- Solution: Invest in continuous education programs aimed at upskilling employees in data analytics, machine learning concepts, and system operation.
4. Resistance to Change
- Solution: Engage employees early in the process by demonstrating how AI technologies will enhance their roles rather than replace them.
Outcomes Achievable Through AI-Based Solutions
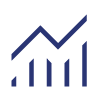
Increased Operational Efficiency
By implementing AI-driven scheduling, our customer saw a 30% increase in efficiency, reducing lead times and improving throughput across their production lines.
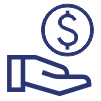
Cost Savings
Through optimized resource allocation, we helped the organization lower operational costs, resulting in savings of up to 20%. These savings were reinvested into innovation and workforce development.
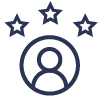
Improved Customer Satisfaction
By ensuring timely deliveries through dynamic scheduling adjustments, we enabled our customer to achieve over 90% on-time delivery performance, significantly boosting customer satisfaction and maintaining their competitive edge.
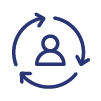
Enhanced Agility
Our AI-powered solution allowed the manufacturer to quickly adapt production schedules in response to market changes, helping them stay competitive while minimizing risks from demand fluctuations or supply chain disruptions.
Conclusion
Despite the challenges associated with implementation- such as data quality issues, integration complexities, skill gaps, and resistance to change- manufacturers that successfully adopt these solutions will position themselves for sustained growth in an increasingly competitive landscape. The outcomes achieved through AI-driven planning not only improve operational performance but also contribute significantly to overall business success by enhancing customer satisfaction levels while driving profitability across manufacturing operations.
Recent Comments